First comes the surface pretreatment, then comes the finish. Why is that? Because the surface of workpieces about to be coated – no matter what material they are made of – require specific pretreatment so that the applied coating adheres perfectly. Or to make it even clearer: Even the best coating gets you nowhere if you don’t use the right pretreatment. Everyone who has ever removed flash rust from a car – and had to do it all over again because they didn't use the right method the first time – is familiar with that problem. But of course this applies not just to rust, but generally to any surface. And not just to preventing corrosion on the surfaces of metals, but to increasing the adhesion of the finish in general – on any material, in any production process. At Venjakob, we always have the right solution. If there’s one thing we’re experts at, it's surface technology. And that means: We understand all the layers below, too. We have mastered the entire structure. Read more to find out what that looks like. If you want to delve even deeper, you can read all about surface treatment here. And if you don’t feel like reading a long text at all, please feel free to contact us in person. We don’t like to sit and read either, we much prefer getting up and getting started. And nothing gets you closer to your goal faster than a personal conversation. When you and we both know what your goals are, we can we achieve them together.
Your products need surface pretreatment, that much is clear. But which method?
Surface pretreatment is a preliminary stage before the actual coating process. However, it can also be used separately for industrial cleaning of workpieces. Pretreatment of workpieces is often indispensable if you want your surfaces to be perfect. First and foremost, surface pretreatment removes contamination. But it also involves activation processes that prepare the surface for the coating material, that is to say: it improves the feel and therefore optimizes the final surface result. For each of these functions, we offer different pretreatment processes, which are usually based on the specific surface properties of the materials. Sometimes aqueous cleaning is required, sometimes it may be CO2 cleaning. The criteria used for your products depend on the degree of contamination – or on the properties of the workpiece material.
Our expertise in surface pretreatment is your key to success!
Venjakob offers innovative system technologies that more than meet the ever-increasing demands on the quality and cleanliness of your products and form the basis for high-quality coating. Our experienced staff will be happy to advise you so that the surface pretreatment system you choose meets your requirements and optimizes your production.
Cleaning, pretreatment, activation – the perfect process technology for any application
From a functional perspective, there are three different types of pretreatment. Cleaning, activation and abrasion. These processes – at least one of them – are required before coating almost any material – be it metal, wood, glass, ceramic or plastic.
Cleaning process
Typical cleaning begins with dust removal or degreasing and sometimes requires blasting or even cleaning using an aqueous solution. At Venjakob we offer all of these processes:
Activation process
Sometimes the surface does not need to be cleaned so much as specially prepared to optimize the adhesion of subsequent coats. Flame treatment, plasma activation and flame silicification are the methods of choice for this task.
Abrasive process
What if normal cleaning isn’t enough? Well, for dirt that simply does not want to detach or for rough and uneven surfaces, we have stronger methods in store. We know all about the perfect pretreatment for any application and will make sure your workpiece gets what it needs.
Polishing, sanding and coating – pretreatment requires expertise
With so many pretreatment processes to choose from, it is ultimately the specific case that determines which pretreatment, which method is the best fit. After all, the process is applied in industrial production. In rare cases you might be dealing with single-piece batches, but it’s usually mass production, production in large quantities, for which the correct pretreatment process must be selected from the range of available pretreatment methods. But whether you’re processing one workpiece or many, what’s essential is achieving the best possible result. This is only possible if all the components of your coating line are perfectly adapted to each other.
Embedded in a comprehensive approach: our process experience
You have probably noticed by now: We don’t view surface pretreatment as an isolated process. We consider all the different processes – the cleaning processes, the activation processes and abrasive processes – primarily as systematic building blocks in a comprehensive process that builds up layer by layer and, at the end of which, a flawless coating is what makes the workpiece what you want it to be: Your product. Thoroughness from start to finish characterizes our method and experience very well. In fact, it describes our entire approach. Just as surface pretreatment takes place before priming, followed by the actual coating process – whether by spray, flow, dip or roller coating – these process steps are integrated into the upstream loading and downstream drying process and packaging or removal. And this complete process sequence, in turn, is based on a prior design and consulting phase and a follow-up maintenance phase (which rarely becomes necessary). Why have we decided to describe this sequence in so much detail? Because it shows you the basis of our collaboration.
And there’s one more thing: Even though we have a comprehensive approach, this does not mean that we are restricted to complete systems all the way from feeding to removal. Many of our customers only need specific modules, mostly core elements. And of course we provide those. But nevertheless, many of these customers were glad that we already had a potential expansion of the plant in mind during design and implementation. You, too, are sure to appreciate that we take a broader view.
So what’s next? Next, let's talk – about surface pretreatment
Yes, about surface pretreatment – and everything else. Reading is good. But talking is better. And doing is best. So let us do what we do best – we mean that as an invitation to achieve your goals together. Simply let us know what you need. Together with you, we will design a system adapted to the workpieces and workpiece quantities you need to process. As a stand-alone solution or continuous flow system. The modular design of our surface pretreatment and cleaning systems allows you to easily expand your system if necessary. This allows you to respond quickly and flexibly to changing requirements in your market. But most importantly – and this is what we are all about – a Venjakob coating system puts you in a position to act from a solid foundation.
Your contact
Simply let us know what you need. Together with you, we will design a system adapted to the workpieces and workpiece quantities you need to process. As a stand-alone solution or continuous flow system.
The modular design of our surface pretreatment and cleaning systems allows you to easily expand your system if necessary. This allows you to respond quickly and flexibly to changing requirements in your market.
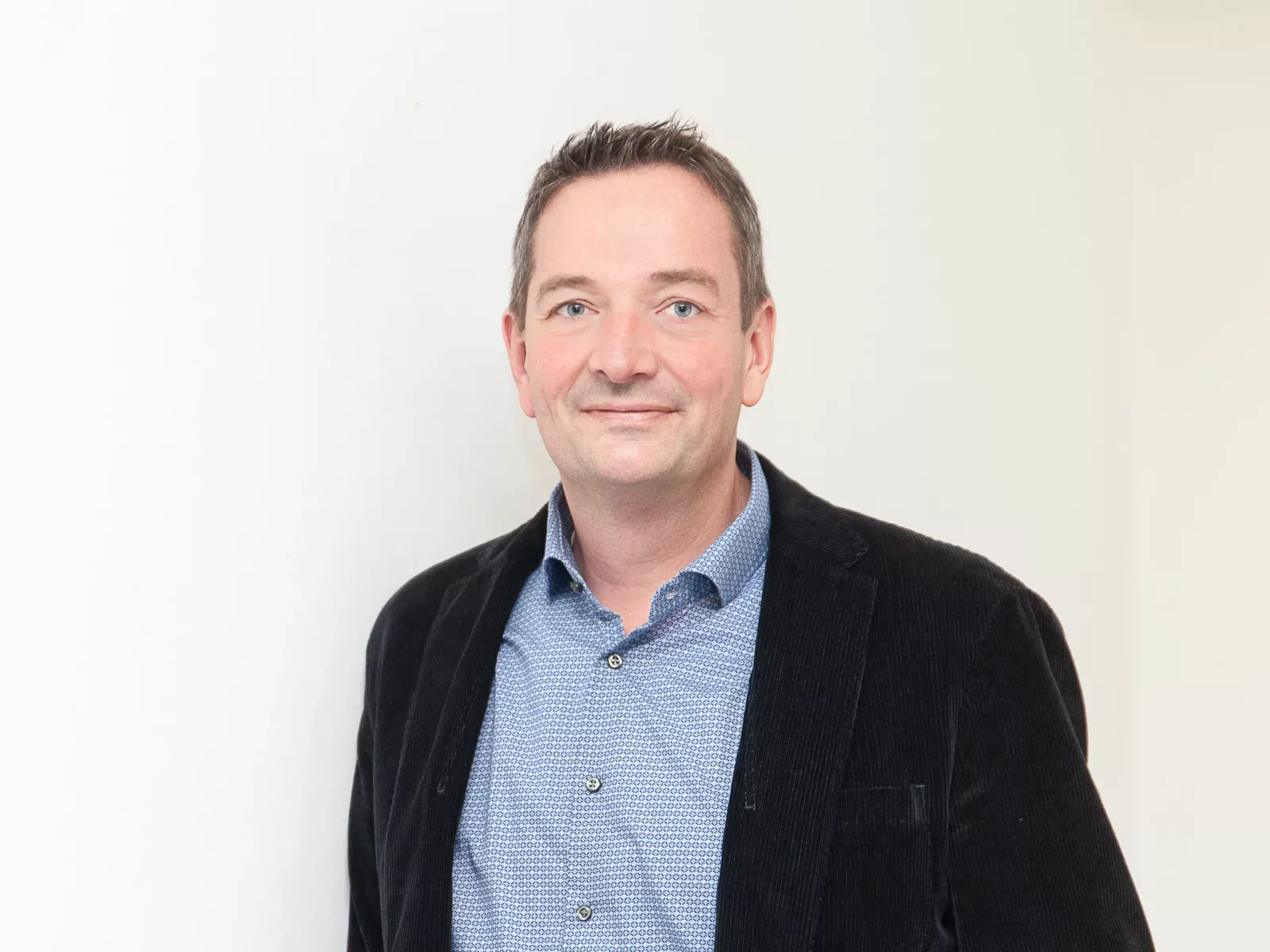
Gert Grosse Deters
General Industry|Automotive
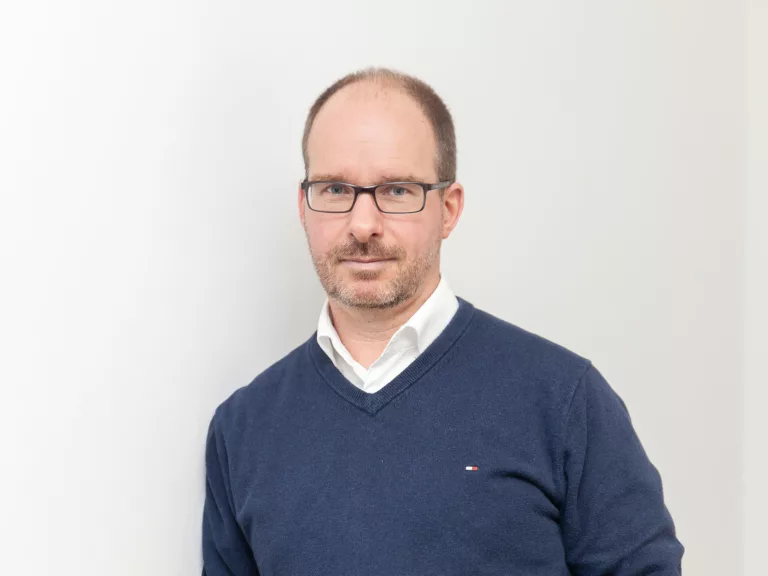
Christian Streit
Wood|Building Materials