- Surface pretreatment
- Cleaning process
- Dust removal and ionization
Dust removal and ionization with Venjakob
How to use ionization and dust removal to prepare surfaces
Dust sticks in place – and it can be very stubborn. But it has no place on surfaces just before they are coated. If you want a brilliant surface coating, Venjakob's dust removal systems and ionization units create excellent conditions for this. While ionization eliminates the electrostatic charge on the component surface, the dust removal system uses blowing nozzles in a blowing system to remove all the dust particles from the surface. Clear the way for coating – through dust removal and ionization. But how does that work exactly? With Venjakob, it works exactly as your application requires. That’s because we develop the exact solution you need, tailored precisely to your processes. No matter what industry you are in.
Why dust removal and ionization are important for a brilliant surface finish
In the run-up to almost any surface finishing process, in almost any application in a wide variety of industrial sectors, dust on the workpieces can become a problem for the intended finishing process. In most cases, simply removing dust from the surface is not enough. Often the existing electrostatic charge requires more than just the use of a dust removal process. While our dust removal systems remove dust particles adhering to workpieces by means of blowing nozzles, ionization devices used in addition act on the electric field of the component surface. After all, it is precisely this electrostatic charge that promotes the adhesion of dust. This is exactly why we at Venjakob combine both processes: first comes ionization, then the dust is blown off the workpiece.
The advantages of customized dust removal systems
Many factors play a role in finding the perfect system for your production: We take all this information into account when integrating the best possible dust removal process into your production flow. After all, our goal is not to offer you just any dust removal system, but give you the solution that will benefit you the most in the long run. That is why we offer a wide range of dust removal/ionization systems adapted to the requirements of your production process. As a rule, all Venjakob dust removal systems have blowing nozzles that remove dust particles from workpieces. Optionally, they can also be equipped with natural bristle brushes. Depending on your requirements, the dust removal systems also include an ionization unit that frees the surface from electrostatic charge so that the dust particles are easier to remove from the surface. We will be happy to coordinate these and other equipment features with you personally.
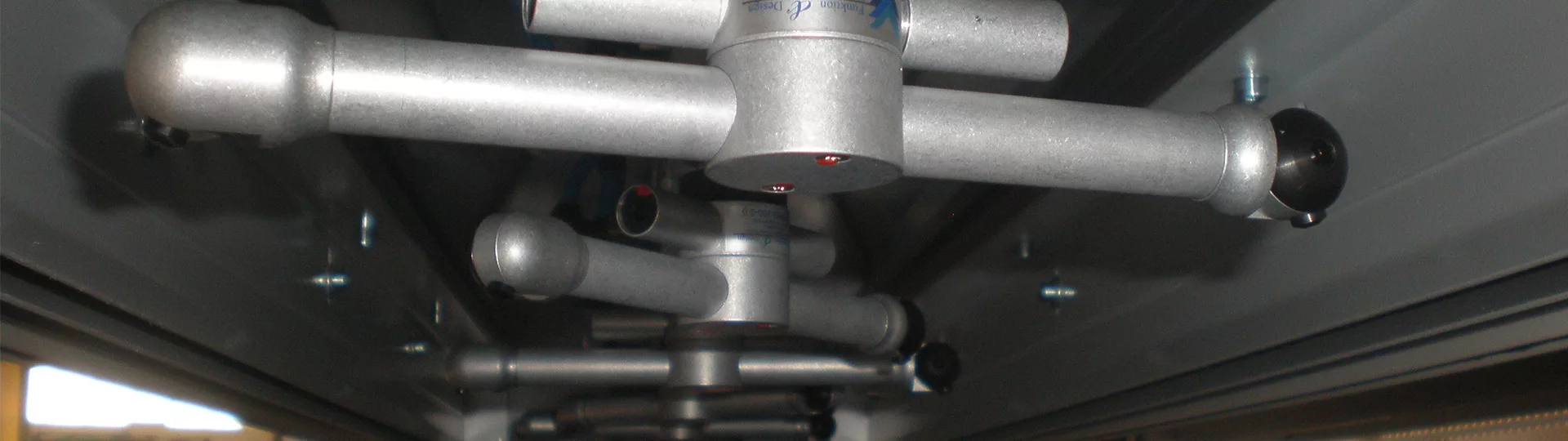
What applications are suitable for dust removal systems and ionization units
We design customized dust removal and ionization systems for removing dust with exhaust air – for dust in particles or large dust volumes and similar foreign objects. These systems are used throughout many industries.
Typical applications for dust removal and ionization can be found, for instance in the
- Wood industry
- Plastics industry
- Glass industry
- Metal industry
- Building materials industry
Dust removal from wooden surfaces
In the woodworking industry – be it in the production of kitchens or home and office furniture, in store and interior fitting or even in yacht fitting – workpieces are almost always sanded first. In the production process, the workpieces then pass through an integrated sanding machine to the downstream dust removal unit before they are subsequently coated or finished. As the wood is processed, very fine particles are released, which are sometimes hard to collect completely – no matter how good your extraction system is. A powerful dust removal system is required to capture and remove these dust particles that form deposits on the workpiece surface. For this use in the woodworking industry, we therefore often offer additional brush units to remove coarse wood chips left behind by upstream sanding or drilling processes from the surface. These brushes are usually made with natural bristles. An extraction system with integrated filtration then discharges the detached dust particles from the system with an optimum degree of separation.
When dealing with plastic/glass and metal surfaces, the primary concern is the removal of particles contained in normal indoor air. The electrostatic charge contributes to even stronger particle adhesion.
All these contaminants must be removed without residues before the coating process begins in order to achieve the best possible surface result.
Materials that require ionization
When handling workpieces made of plastic, granules or metal, the primary objective is to remove particles from the component surface. The electrostatic charge of the components contributes to even stronger particle adhesion. In this case, ionization is strongly advised in addition to dust removal because it affects the electrostatic energy of the components. But how exactly does this affect different materials?
Glass pretreatment
Particularly in the coating of decorative glass, functional glass, architectural glass or safety glass, the varying cleaning requirements in the production process must be taken into account for applying materials such as sol-gel for reflection reduction or hydrophobization and hydrophilization. Dust removal is a crucial step that is absolutely indispensable prior to the actual coating process.
The requirements for coating plastics
High-quality coatings applied to plastic are a similarly complex field of application. Many products used in household technology and entertainment electronics, small and large electrical household appliances have a coating. This is yet another field in which dust removal and ionization is indispensable if you want a high-quality coat.
Dust removal for coated metal
Dust removal is likewise essential for coating metal. This is because pipes, wheels, steel plates, beams and housings often require surface pretreatment, depending on the production process and intended use. This pretreatment may involve dust removal.
Equally relevant for building materials
Dust removal may also be required for building materials such as facade cladding, acoustic ceiling tiles and insulation materials – to name just a few. The surface pretreatment method depends on the application and the requirements.
What is essential is product quality
Ultimately, it is important to remove all these contaminants without leaving any residue before the coating process begins in order to achieve the best possible surface results. Only then is it possible to achieve a perfect coating quality. The design of the processes varies from plant to plant, from application to application. At Venjakob, we focus on your specific requirements.
Stand-alone, integrated in your processes or added later
In general, our customers always receive a complete solution from us, including all components. We offer systems – not from a construction kit, but custom-designed for the specific coating task. But often there is already an existing coating system. In those cases, retrofitting is an option – or you could get a stand-alone solution. Whatever your case may be, we will help your production stay flexible.
Good to know: Information about cleaning, dust removal and ionization
To summarize: Foreign components have no place on surfaces that are about to be coated. The issue of how to perform cleaning and removal and what can happen in the process also depends on whether the only thing on the workpiece surface is dust. It is necessary to consider that an electric field sometimes forms on a surface, which makes it difficult to easily pick up the dust particles. This problem can be solved through ionization, which removes the electrostatic charge of the particles so that separation is possible with a fan or with blowing nozzles.
So what’s next? Next, let’s talk about dust removal and ionization
Your Finishing Line – Our Process Experience. That is what Venjakob is all about. Much of this process experience relates to the steps that precede the actual coating process. The cleaning processes that precede coating involve a high degree of complexity. Depending on the materials – be it wood, plastic, glass, metal or other building materials – and depending on the end products, the production lines and process steps vary wildly. The process depends on a wide variety of parameters. What is required is know-how, starting with knowledge of a diverse range of cleaning, activation and pretreatment processes. Dust removal and ionization are just two methods. If you want to find the right solution for this step, you have to understand which process to use at what point in the overall concept of a plant. This requires not just knowledge, but above all trust. And it is precisely this – this special trust – that characterizes the experience of working with Venjakob. For proof, look no further than the countless customer projects we have implemented successfully. If ionization and dust removal – or more generally cleaning processes in the context of a coating or finishing project – is a topic you’re interested in, let's talk! And better yet: Let’s do more than just talk! Let's get started with your project! Because we know our business. And yours.
Your contact
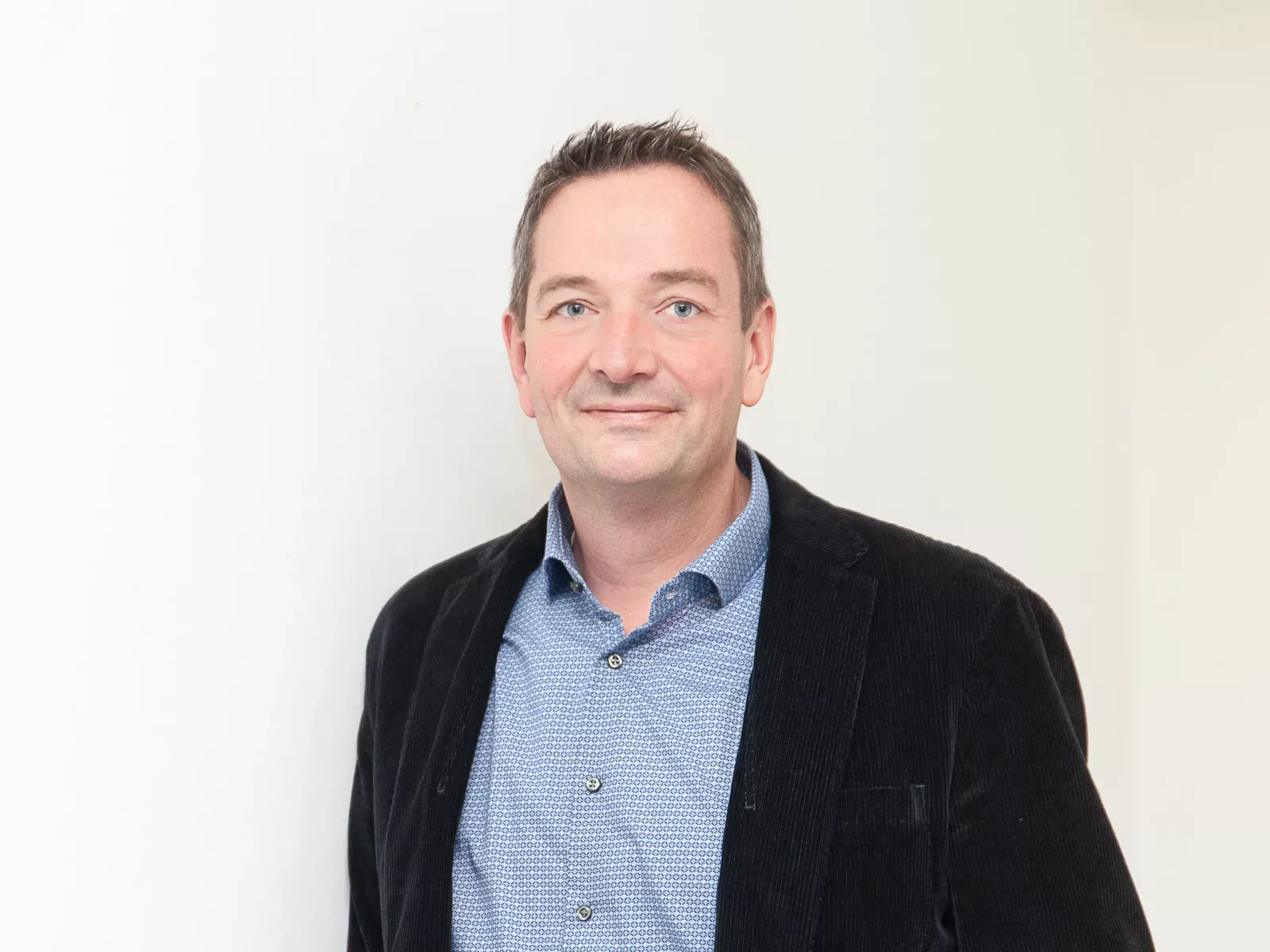
Gert Grosse Deters
General Industry|Automotive
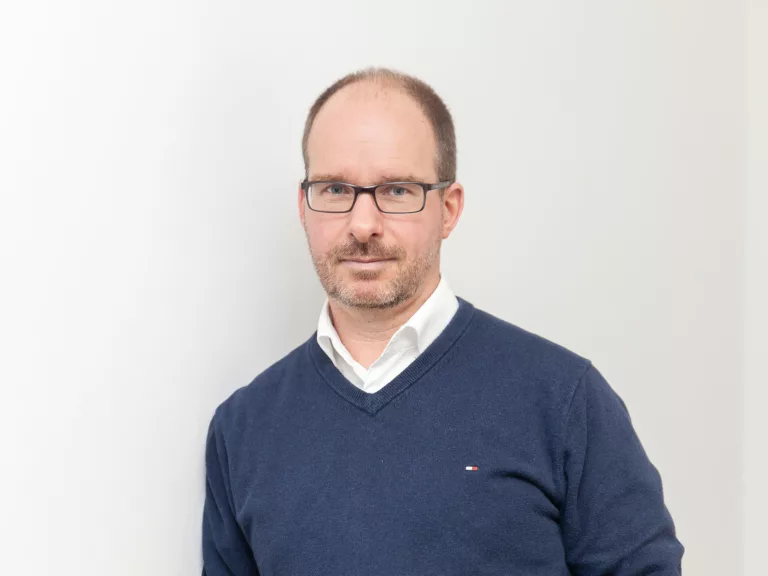
Christian Streit
Wood|Building Materials