- Venjakob
- solutions
- Finishing | Coating
- Flow coating | Dip coating
FLOW COATING AND DIP COATING
Are you now wondering what the differences are between these two processes?
During dip coating, the workpiece carrier with the workpiece is immersed in the coating material to ensure uniform coating. This method is particularly suitable for complex shapes and delicate surfaces. Dip coating reaches hard-to-reach areas, resulting in a uniform and long-lasting coat.
During flow coating, the coating material runs over the workpiece and excess material is removed with air. With our flow coating systems,
you can coat or waterproof your workpieces in an excess material process. Flow coating is particularly suitable for the application of waterproofing, glazes, or primers with a low solids content.
Flow coating
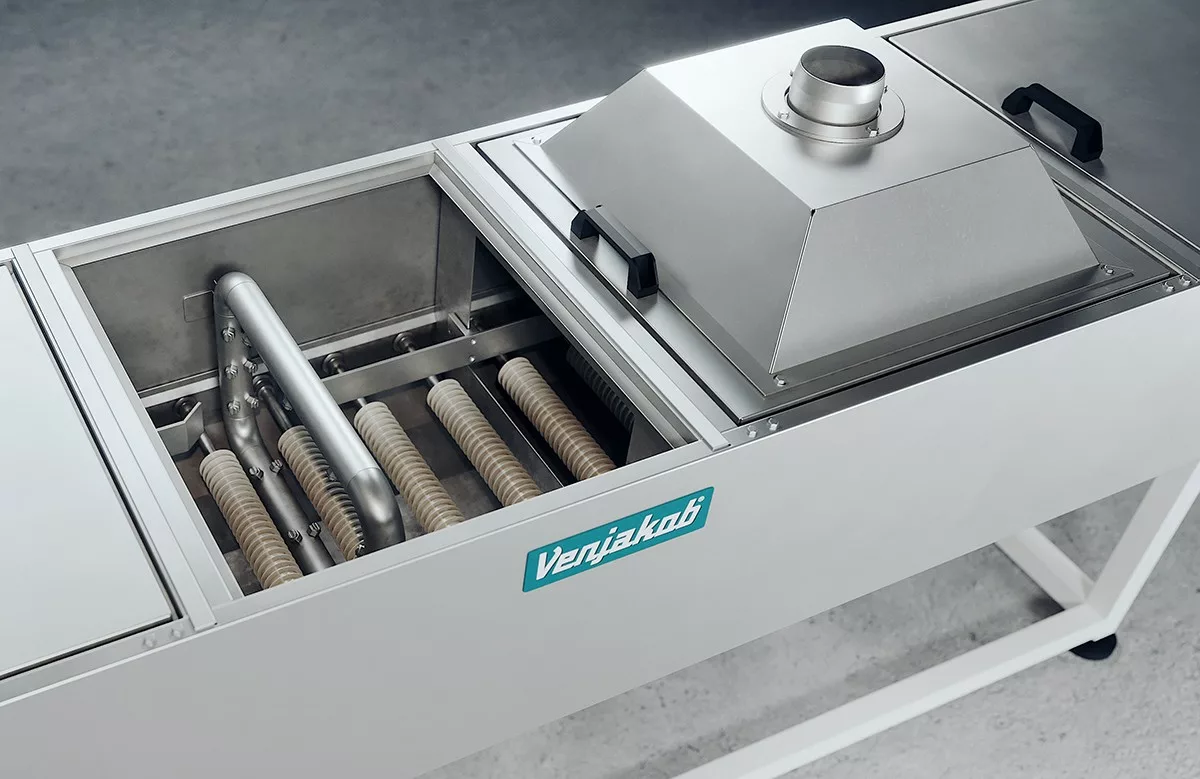
Flow coating for effective four-sided coating
Two different coating methods exist in flow coating: continuous flow coating systems and immersion flow coating. The workpieces being processed are flooded with large quantities of the coating material. The application efficiency achieved with this flow coating process is high and the excess material is blown off the workpiece as it is discharged and can then be reprocessed and reused.What makes Venjakob flow coating concepts so special
With our flow coating systems, you can coat or waterproof your workpieces in a highly effective and sustainable manner with an excess material process. The excess coating material is blown off the workpiece. It can be filtered and reprocessed and is then suitable for reuse. The Venjakob flow coating process offers high throughput rates and achieves an application efficiency of nearly 100%. Our plants are built to the highest quality. They are low-maintenance and offer high system availability.
Applications for the flow coating process
The flow coating process is particularly suitable for coating wooden parts that are not suitable for dip coating because of their tendency to float. This includes:
- Exterior window parts
- Building profiles
- Profiles & moldings
APPLICATION MEDIA
- Low-solid coating materials
- impregnations
- glazes
- primers
Process description – flow coating process
- Loading of individual workpieces (manually or automatically) or feeding from existing production line
- Coating with the excess method
- Recovery via blow-off unit to draining position with recirculation to the dip tank
- Drying in the downstream four-sided dryer (from below and above)
- Removal of workpieces - manual, automatic or transfer to a production line
Advantages of the flow coating method
- Simple machine for high throughputs
- Application efficiency of almost 100%
- Suitable for materials that float
Dip coating
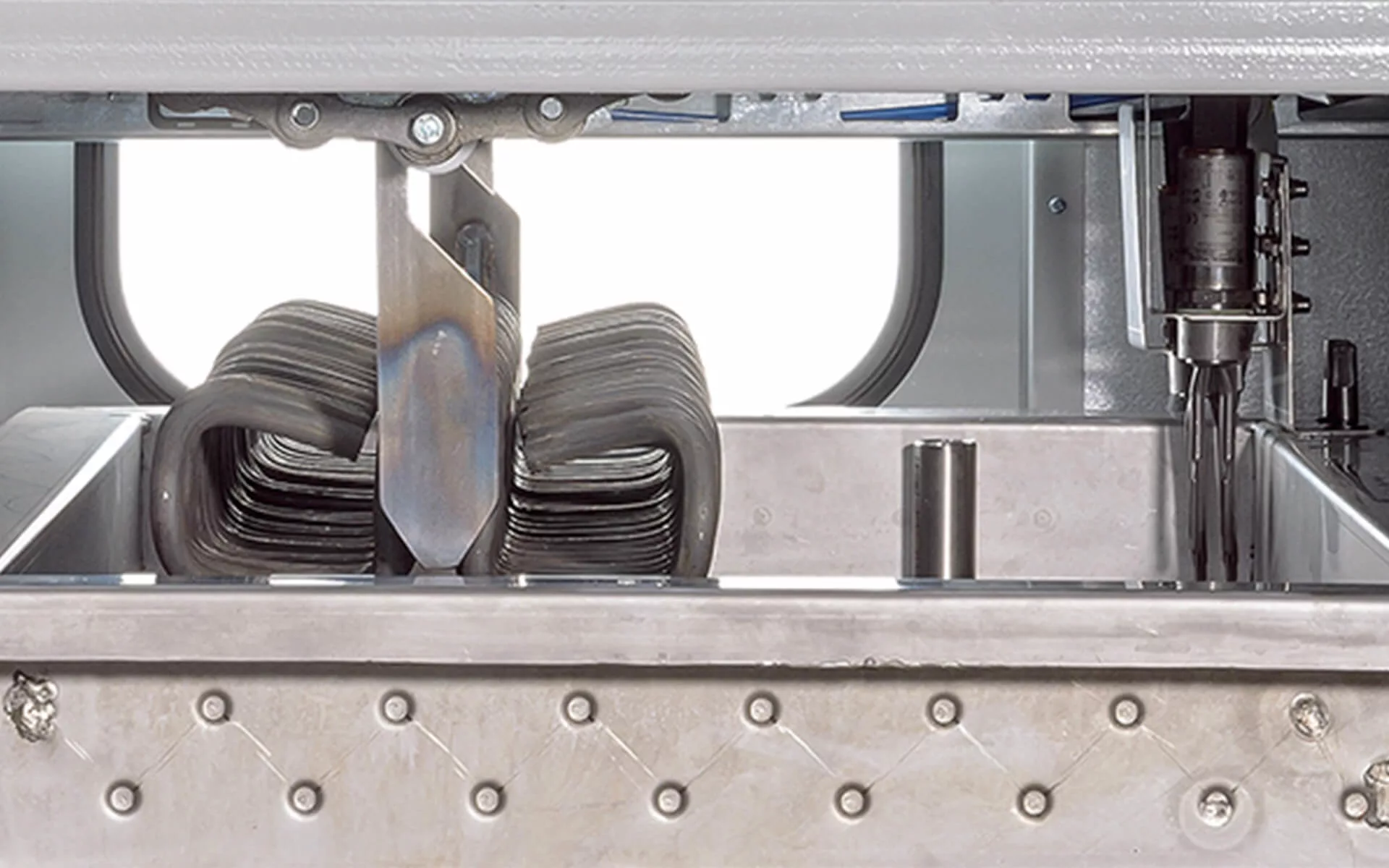
Dip coating, a powerful alternative application method
Our dip coating system is designed for the application of wet coating systems. In the Venjakob dip coating process, workpiece carriers with workpieces are immersed, not poured into a dip tank|drum, as is a common alternative method. The workpieces being coated are transported in a suspended position.
This makes Venjakob dip coating concepts so unique
With our dip coating equipment, you can coat your metal and steel parts easily and effectively. Dip coating also achieves high throughput rates and a great application efficiency. Resource-saving reuse of the drained coating material is possible to a limited extent and depends, among other things, on the properties of the material used.
Our plants are built to the highest quality. They are low-maintenance and offer high system availability. The size of the dip coating system depends on the coating material, the equipment, the workpiece size and the feeding unit. The system can be loaded manually or automatically and is based on the upstream and downstream workpiece flow. At Venjakob we offer a variety of handling technologies and conveyor systems for this purpose from our own production range. Other system modules, such as drying technology or material supply, are also precisely tailored to your requirements.
Areas of application for dip coating
- Steel parts
- Metal parts
Functional coatings are applied to, for instance, protect against corrosion, while decorative coatings are applied to enhance the value of the workpiece.
Application media
- Water-based coatings
- Solvent-based coatings
Dip coating process description
- Feeding of individual components or workpieces on workpiece carriers via a customer-specific feeding device, a robot or manually.
- Transport: chain conveyor or specific conveyor system.
- Dip coating with mobile dip tank
- Draining at draining position with recirculation to the dip tank
- Drying in the integrated drying channel adapted to the coating system
- Removal either via the feeding device, or via a removal device, a robot or manually.
Advantages of dip coating
- Simple machine for high throughput
- Application efficiency of almost 100%
So what’s next? Next, let's talk about flow and dip coating
To summarize: Both application methods are effective and suitable for high throughput. Moreover, both achieve a high application efficiency. You already have a flow or dip coating system in use and would like to replace your systems? Or are you considering investing in this automated coating technology for the first time and are looking for a strong, reliable partner? Then let's talk!
Why should you choose a flow coating or dip coating system from Venjakob? Because we offer world-class solutions for your coating needs! Our machines are precise, reliable and state of the art. With our many years of experience and our expertise, we can provide customized solutions for your specific needs. You can trust in Venjakob to create efficient, top-quality coating processes for you.
Your Finishing Line. Our Process Experience.
Your contact
Our in-house technical center makes it possible to test processes under realistic conditions. Simply tell us what you need, get your material supplier involved, and we will develop a solution together with you.
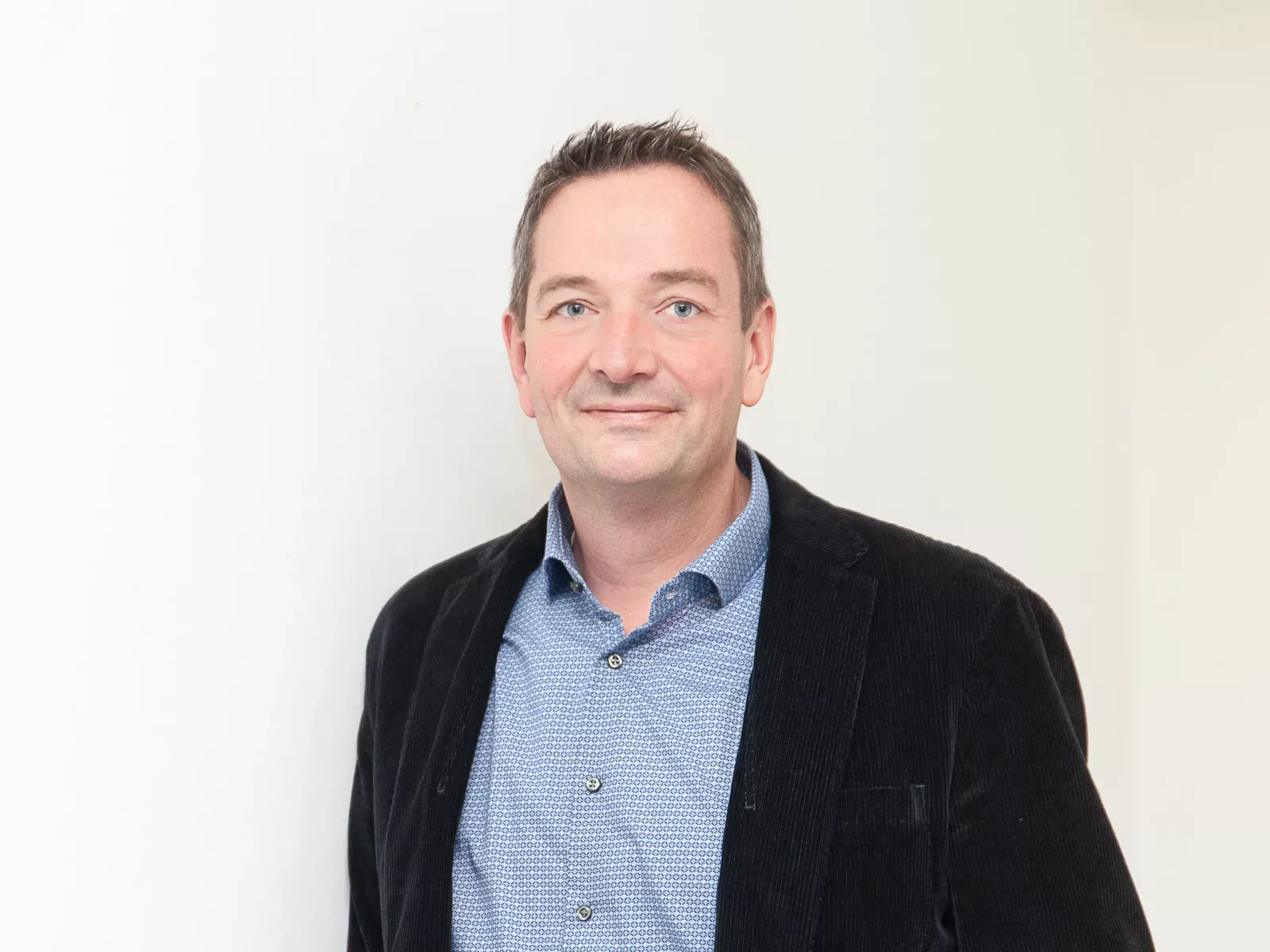
Gert Grosse Deters
General Industry|Automotive
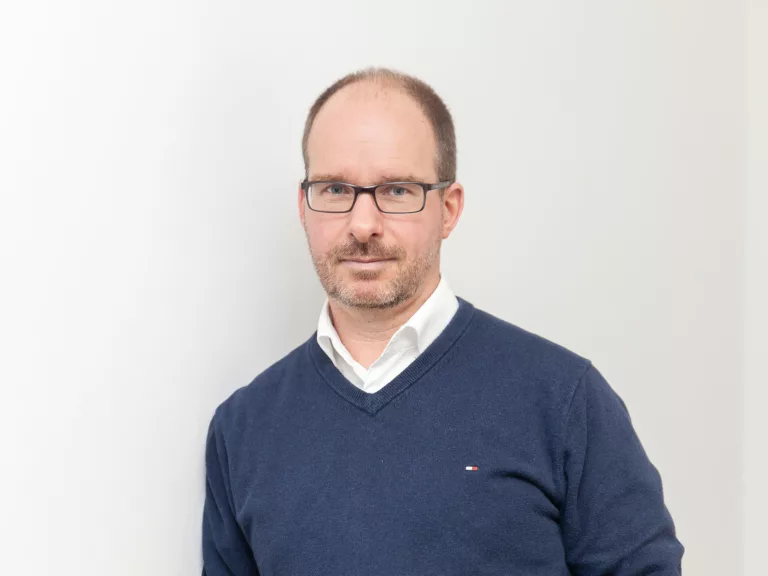
Christian Streit
Wood|Building Materials