We’re at your side when you need us – without travel expenses
Well, we won’t be able to shake hands. But you won’t have to deal with travel times and travel expenses. And we are by your side when you need us. We would also like to mention: The remote maintenance experience has long been nearly as personal and pleasant as in-person visits on site. To sum it up: Venjakob’s digital services can be accessed more quickly, save costs and are efficient and effective. They even protect the environment! But digital services are of extraordinary importance for yet another reason: They are proof of Venjakob's innovative spirit and a demonstration of our technological expertise: After all, you rightfully expect our systems to reflect both – so neither must be missing from our services. After all, it is precisely this that increases the availability of your system and boosts your productivity in the long term.
Remote service
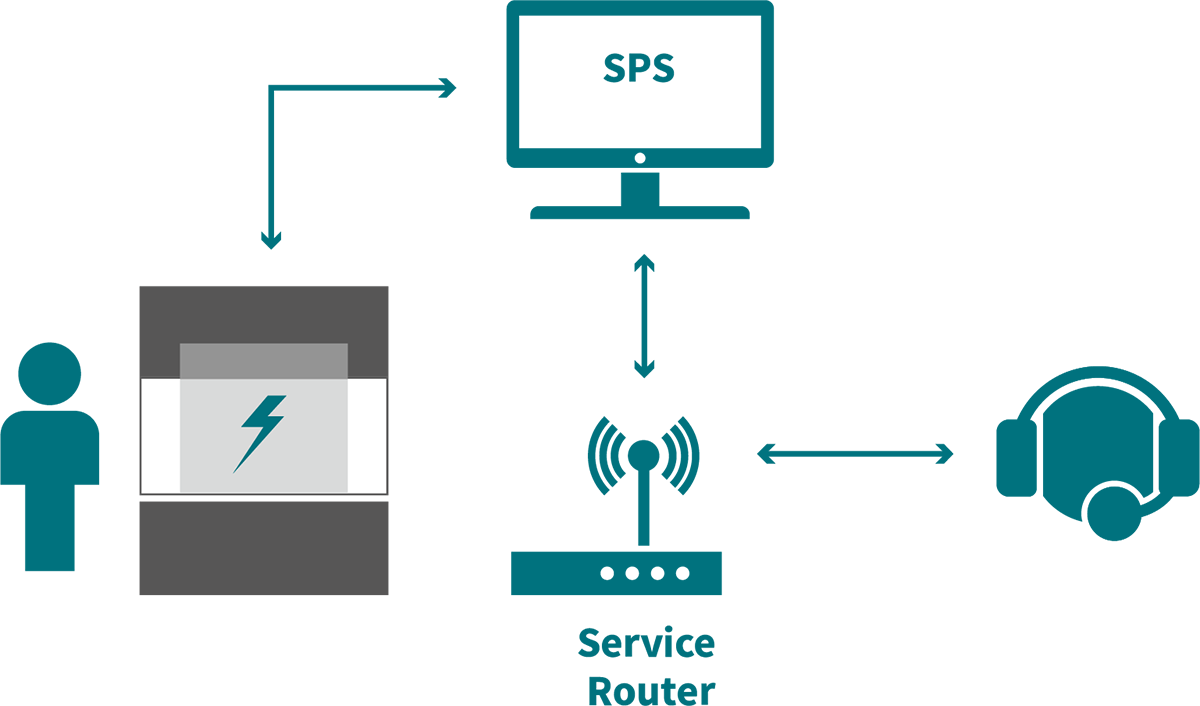
Maintain, optimize, prevent damage – via remote access to the plant control system
Venjakob uses remote service, among other things, for remote maintenance as part of your maintenance agreement . You allow our service staff remote access to the control system of your plants in order to carry out optimizations, detect incorrect settings at an early stage and – if possible – prevent damage before it occurs. And if a system malfunction does occur, our remote service is on the spot faster than a service employee could ever be.
Remote service in a malfunction – step by step
- If a malfunction occurs, contact us: You can reach our service team by phone or e-mail.
- Our service team then takes over the plant control system via remote access and diagnoses the fault together with your plant personnel.
- Any incorrect settings will be corrected directly by our service team or they will specifically instruct your specialist personnel to make any necessary corrections.
- We analyze more complex incidents with the aid of augmented reality, using our AR service app.
Remote services at a glance
- Remote maintenance of machine and plant networks
- Optimization, operating data acquisition and troubleshooting
- Direct interaction with connected devices
- Secure communication
- Remote access to USB devices
- High-performance hardware platform
- OpenVPN with server and client support
- Variable connection to the internet
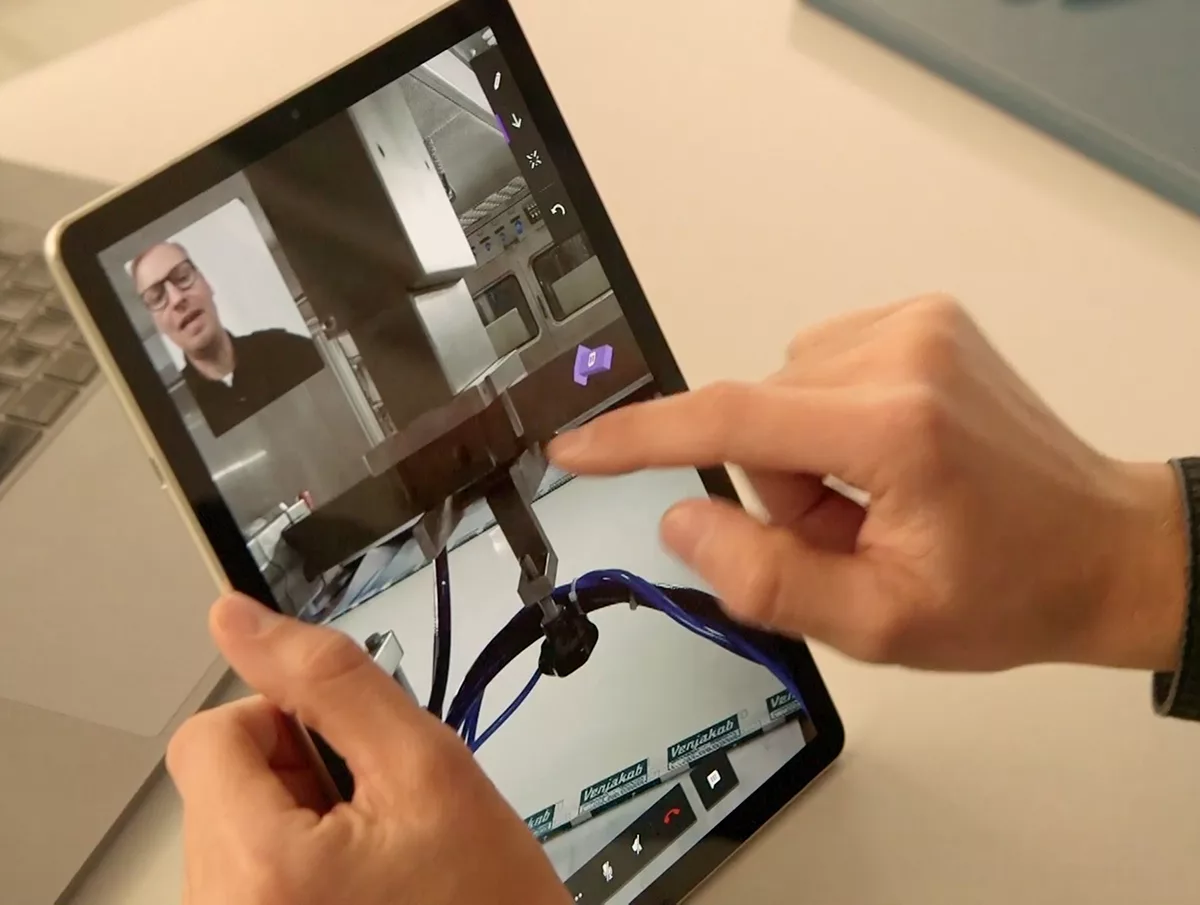
AR service
Smart, instant, helpful – video calls with augmented reality
The advantage of our AR service app: We see the incident through your eyes. Meaning: Our augmented reality application shows us exactly what you see – and together we solve what your plant staff can't solve alone. In real time. Without language barriers. Without misunderstandings. Just as if our service team were right there with you. AR – Augmented Reality – is ideal for analyzing complex system malfunctions, for troubleshooting, and for assisting plant personnel with troubleshooting. At Venjakob, we also use AR to support our own fitters during plant commissioning. When we provide support, we make the video call using AR glasses (smart glasses), a smartphone or a tablet.
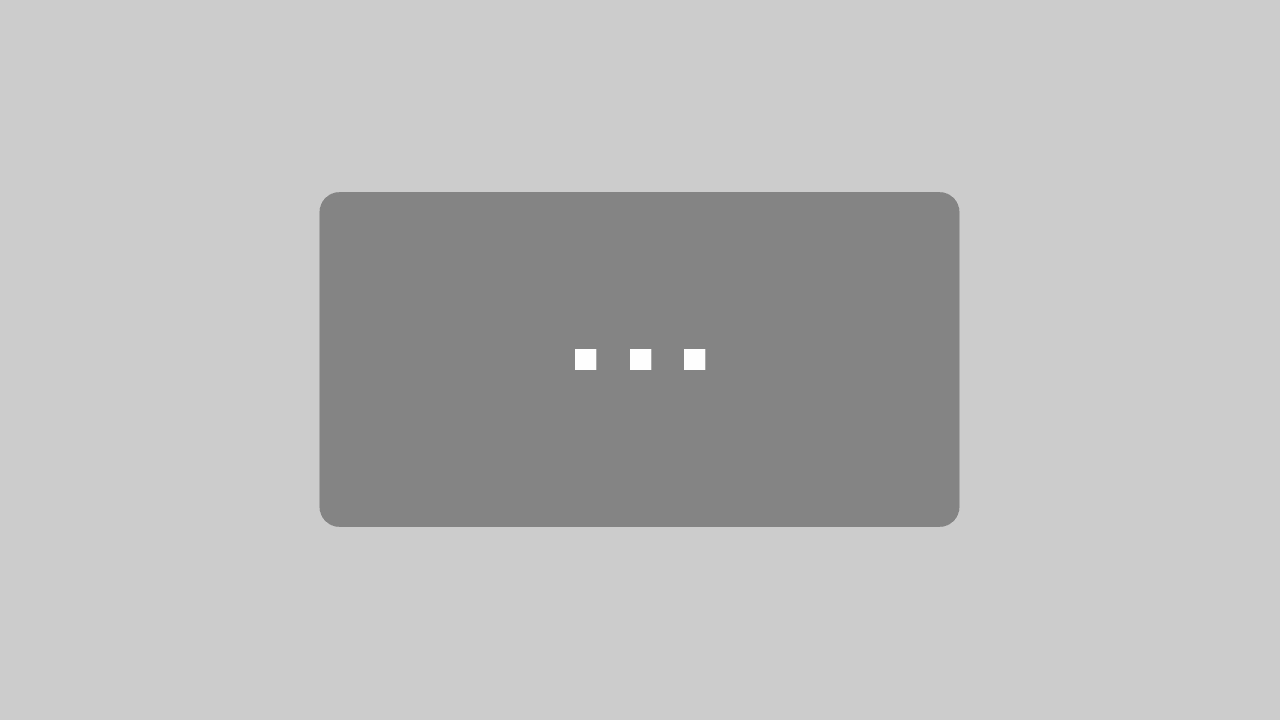
Mit dem Laden des Videos akzeptieren Sie die Datenschutzerklärung von YouTube.
Mehr erfahren
The AR service app in use
- As we mentioned above: If a malfunction occurs, contact our Venjakob service team – via e-mail or by phone.
- Simply describe your concern and arrange a callback appointment.
- Your plant staff receive our callback via smart devices – smartphone, tablet or AR data glasses – and start our AR service via the app.
- Once the video call connection is established, our service team sees exactly what your plant personnel see.
- The image transmission allows our service team to provide targeted support to your system personnel during troubleshooting and to guide them through the troubleshooting process – using speech, pointers, text inputs and symbols.
- The video call can also be recorded to document the case.
AR Service Flyer: Download now
AR service at a glance
- Support with troubleshooting
- Reduces machine downtime
- Support by qualified personnel
- Reduction in time and cost (no travel)
- Service employee sees actual situation of the plant at the customer's facilities
- Reduced language barrier thanks to visual representation
- Display of machine-relevant data (drawings, machine parameters)
- Calls / videos can be recorded for documentation purposes
Your contacts
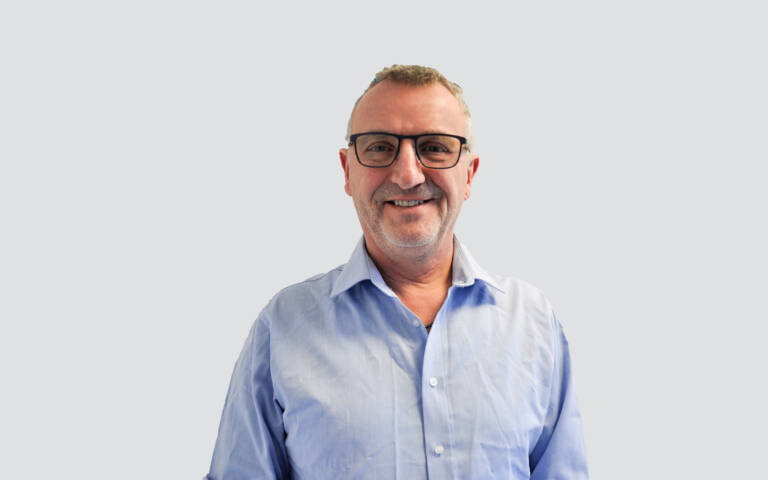