Oberflächenbeschichtung von Kunststoffteilen – Zeiträuber im Fokus
Zukunftsfähige Lackieranlagen zeichnen sich aus durch Wirtschaftlichkeit sowie ein Höchstmaß an Flexibilität mittels des Einsatzes intelligenter Steuerungs- und digitalisierter Kommunikationssysteme. Das Modulkonzept von Venjakob erlaubt zudem eine bedarfsgerechte Ausstattung der einzelnen Maschinen, die jederzeit durch zusätzliche Funktionen aufgerüstet werden können.
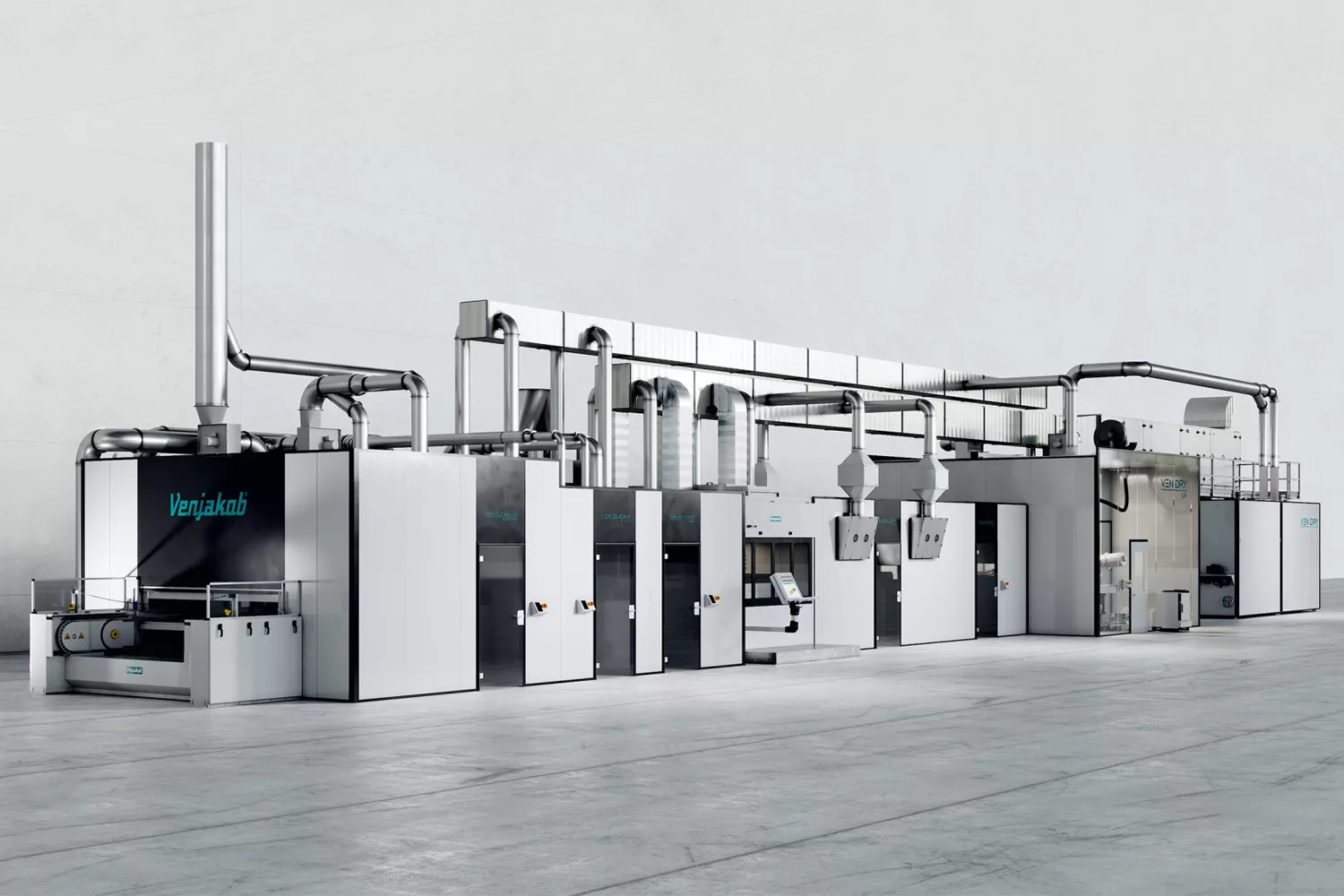
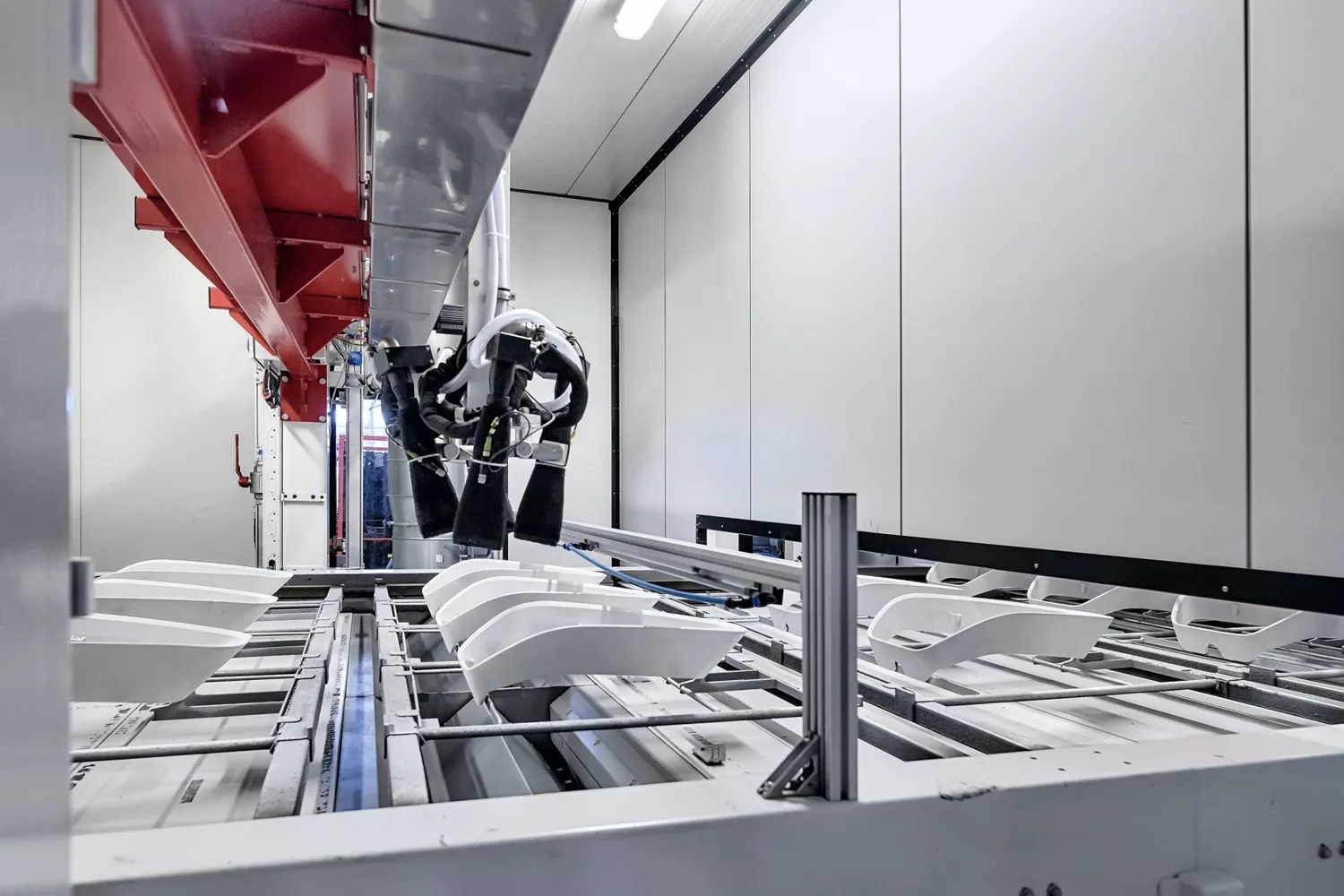
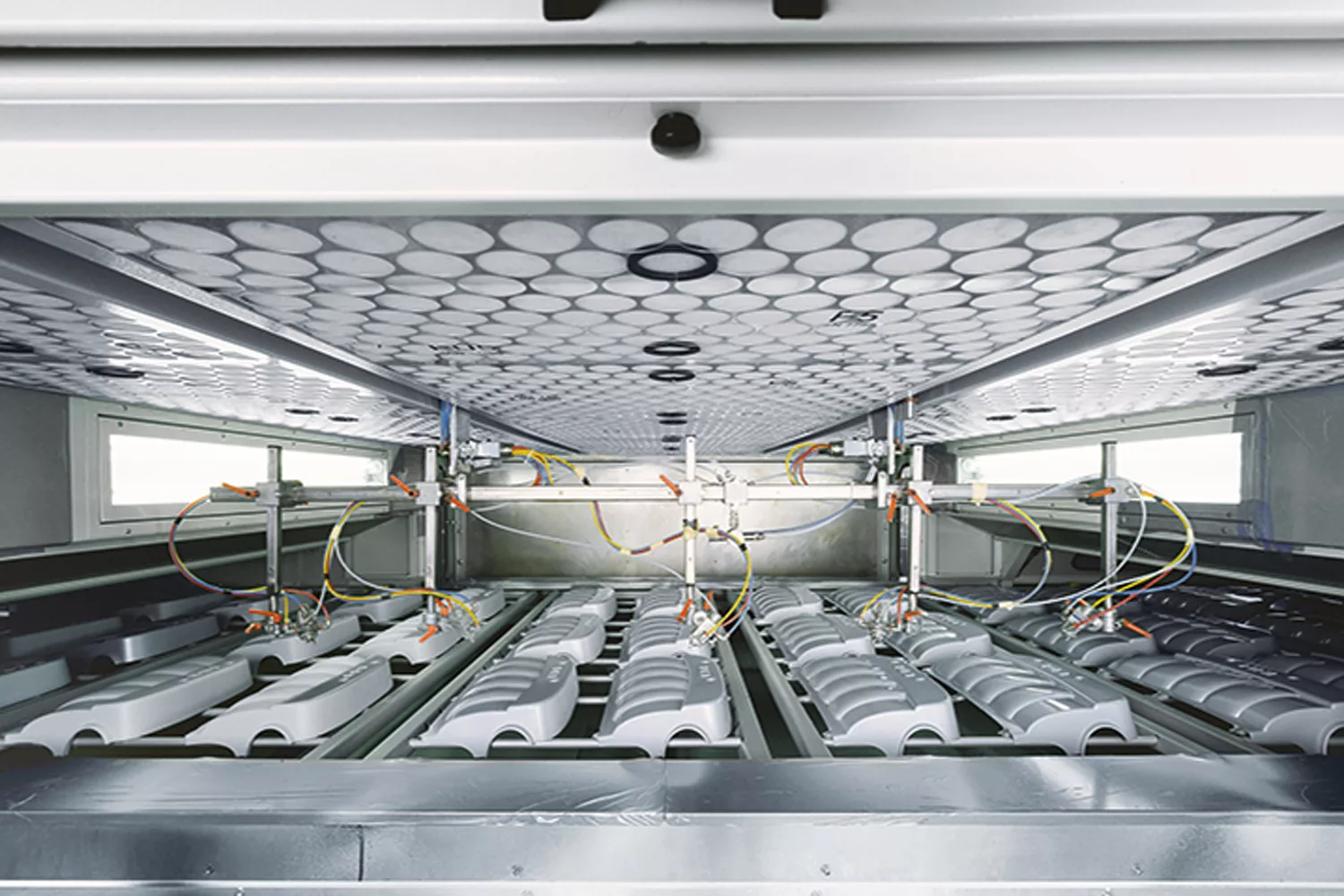
Die Oberflächenbeschichtung in der industriellen Fertigung von Kunststoff-Komponenten u.a. für Automotive gehört zu einem wichtigen, womöglich sogar zum wichtigsten Part innerhalb der gesamten Produktionskette. Hier kann viel Geld ausgegeben, ebenso viel auch eingespart werden. Teure Lacke, zeitaufwändige Maschinenreinigungen, Einhalten von Umweltvorgaben sowie sich stets verändernde Trends bei Materialien und Lacken erfordern eine technische Ausstattung, die dem Anwender über die Jahre hinweg die geforderte Flexibilität und damit auch Investitionssicherheit bietet.
Gesamtkonzept mit optimierter Individualausstattung
Das hier beschriebene Gesamt-Anlagenkonzept zur Oberflächenbehandlung dient als Beispiel dafür, was moderne Lackieranlagen zu leisten vermögen. In der Anlage werden unter Verwendung von Nasslacksystemen, Kunststoffteile lackiert und getrocknet. Die einzelnen Maschinen – von der Vorbehandlung über die Lackierung bis hin zur Trocknung – wurden mit einer optimierten Individualausstattung versehen und zu einer Gesamtanlage zusammengesetzt. Verwendet werden können traditionelle 1K- und 2K-Lacke auf Lösemittel-Wasserbasis sowie UV-Lacke.
Die Gesamtanlage kann mit folgenden Modulen konfiguriert werden:
- Reinigungsmodule: CO2-Reinigung, Hochleistungsentstaubung/Ionisierung
- Aktivierungsmodule: Beflammung, Plasma, UV
- Beschichtung: Lackierkabine
- Trocknung: Abdunstzone, Infrarot-Trockner, UV-Trockner, Umlufttrockner, Kühlzone
- Frischluftversorgung: Zuluftanlage, Vollklimatisierung
- Abluftreinigung: Abluftreinigungsanlage RNV, TVA
Zentrales Bedienpaneel für alle Maschinen
Über das anlageninterne Kommunikationssystem (Ethernet) sind sämtliche relevante Systemparameter verfügbar und können über ein zentrales Bedienpaneel der Anlage vorgewählt und eingestellt werden. Das ermöglicht ein flexibles Zusammenspiel aller einzelnen Komponenten. Jedes Produkt erhält sein eigenes Rezept. Jede Farbe kann parallel zur laufenden Produktion vorbereitet und innerhalb kürzester Zeit aktiviert werden.
Hohe Verfügbarkeit der Anlagen
Hinsichtlich der Amortisation der Anlageninvestition legte Venjakob bei der Planung der hier vorgestellten Produktionsstraße den Fokus auf eine möglichst hohe Variabilität bei der Nutzung der eingesetzten Maschinen. Entsprechend wurde die technische Ausstattung gewählt. Dabei nahm man insbesondere den Vorgang des Spritzlackierens in den Fokus. Für das Spritzlackieren typisch ist die Aufteilung der Gesamtproduktionszeit in Produktion und Reinigung. Hier wird festgelegt, wie effizient und profitabel die Anlage arbeitet. Die Vorteile der modulartigen Bauweise werden bei der Spritzlackieranlage daher besonders deutlich. Wichtige „Zeiträuber“, wie Farbwechsel können parallel zur Produktion stattfinden und schnellstmöglich mit minimalem Stillstand des Transportes durchgeführt werden.
Unverzichtbar: Maschinen- und Prozessdaten
Informationen über die Prozesse, die Produktivität der Anlage sowie Kenndaten, die den Verschleiß dokumentieren, sind unverzichtbar für die gleichmäßige Produktionsqualität, die logistische Planung und die Instandhaltung der Anlage. Zu den Vorteilen der Prozessdaten-Erfassung gehören:
- Die Instandhaltung wird mittels der Kenndaten über notwendige Verschleißarbeiten informiert, bevor die Anlage aufgrund einer Havarie angehalten werden muss.
- Die Produktionsleitung erhält verlässliche Daten über die Produktivität und kann so die vorgegebenen Ziele einhalten.
- Stoffflüsse und Bedarfsmittelplanung fallen innerhalb des vernetzten Informationsnetzes leichter, da ein Bedarf frühzeitig erkannt wird.
- Die gesamte Zuführ- und Abführlogistik kann flexibel geplant werden, da die Produktivität bekannt ist.
Prozess-Schritte in der Oberflächenbehandlung
1. Materialhandling
Am Einlauf der Maschine werden die Bauteile, die auf spezifischen Teileskids liegen, in horizontale Lage auf die Transportpalette gebracht und später an derselben Stelle als fertiges Bauteil entnommen. Wird eine umseitige Beschichtung der Werkstücke gewünscht, kann dafür optional eine Drehvorrichtung installiert werden.
Die Förderkette des Palettenförderers fährt mit gleichbleibender Geschwindigkeit durch alle Anlagenkomponenten. Das wurde insbesondere für die Abdunst-Trockenstrecken so programmiert, damit die gewünschten Behandlungs- und Haltezeiten erreicht werden.
Vorteilhaft ist, dass mit diesem Palettenförderer platzsparende Anlagenkonzepte möglich sind. Dies bezieht sich zum einen auf den Hochtrockner, der den Raum in die Höhe nutzt, anstatt sich in der Länge auszubreiten. Die Paletten werden im Umlauf, nach dem Paternoster-Prinzip befördert.
2. Die Vorbehandlung der Bauteile
Die vorgelagerte Vorbehandlung befreit die Werkstückoberflächen mittels flüssigem CO2 kontaktfrei von Verschmutzungen. Nachfolgend wird eine Hochleistungsentstaubung/Ionisierung mit verbrauchsoptimierten, rotierenden Abblasdüsen eingesetzt. Die aufgewirbelten Partikel werden über ein effizientes Absaugsystem entfernt. Der Reinigung folgt ein Neutralisieren der statischen Oberflächenladung der Werkstücke über ein Ionisiersystem. Die Werkstücke verlassen die Vorreinigung in einem sauberen und ladungsneutralen Zustand.
3. Die Aktivierung der Bauteile
Eine Oberflächenaktivierung zur besseren Benetzbarkeit mittels Beflammung, Plasma oder UV könnte ein nächster Schritt in der Vorbehandlung sein. Die genannten Verfahren erhöhen die Qualität der Haptik und bereiten die Kunststoffwerkstücke optimal auf die Aufnahme des Beschichtungsstoffes vor.
4. Spritzlackierung
Die Lackieranlage fördert die Bauteile auf einem Teileträger abgestimmten Transport unter den, sich quer zur Laufrichtung bewegenden, Lackierpistolen hindurch. Lackiert wird im Durchlauf, ohne zu stoppen. Die Maschine kann mit einem automatischen Farbwechselsystem ausgestattet werden. Im Zusammenspiel mit der übergeordneten Anlagensteuerung erfolgt der Farbwechsel automatisch.
Die Zuleitungen zwischen dem System und den Spritzpistolen wurden kurzgehalten, um unnötige Lackverluste beim Spülen zu vermeiden. Das Color-Management-System von Venjakob sorgt zudem für kürze Rüstzeiten und einen geringeren Verbrauch von Lösemitteln.
Ein anwendungsadaptiertes Absaugsystem ermöglicht im Zusammenspiel mit einer ausgeklügelten Frischluftversorgung ein optimales Abführen des entstehenden Oversprays. Die Werkstücke werden einlaufseitig mittels eines Werkstückscanners erfasst und die Maschinensteuerung erstellt für jede installierte Spritzlackierpistole ein verbrauchsoptimiertes Spritzlackierprogramm.
5. Trocknungsprozess
Die anschließende Abdunstzone ist der Länge nach auf den Lackierprozess und die damit verbundene Lackiergeschwindigkeit ausgelegt. Ebenfalls ist es möglich, in die Abdunstzone eine Infrarot-Trocknung zu integrieren. Ebenso wählbar ist eine nachgeschaltete UV-Trocknung mittels Roboter, der sich quer zur Förderrichtung bewegt. Der sich anschließende Umlufttrockner ist auf sechs Etagen ausgelegt und durch verfahrbare Trocknerelemente zu Reinigungs- und Wartungszwecken leicht zugänglich. Die Trocknungszeit und damit verbundene Größe (Länge) des Trockners ist auf den Lackierprozess abgestimmt. Unterhalb der Anlage gibt es eine Kühlzone. Dort werden die Bauteile wieder zum Einlauf der Lackieranlage gefördert. Optimales Abdunsten, Trocknen, Härten oder Kühlen sind wichtige Prozessschritte, wenn es darum geht, eine hohe Oberflächenqualität zu erhalten.
6. Frischluftversorgung
Die Versorgung mit Frischluft erfolgt unabhängig von der Halle. Die Zuluftanlagen saugen die Luft von außen an, filtern, erwärmen und befeuchten diese abgestimmt auf die klimatischen Bedingungen der zu verarbeitenden Lacksysteme. An einigen Standorten sowie beim Einsatz verschiedener Lacksysteme ist eine Vollklimatisierung der Zuluft Voraussetzung, um die klimatische Bedingungen beim Lackieren ganzjährig konstant zu halten. Die Vollklimatisierung kann jederzeit in die Zuluftanlage integriert werden.
7. Abluftreinigung
Die Abreinigung von organischen Lösemitteln aus der Abluft der Gesamtanlage wird über eine Abluftreinigungstechnik aus dem Hause Venjakob Umwelttechnik sichergestellt. Diese wird passend abgestimmt und ausgelegt auf den Lösemittelverbrauch und das Abluftvolumen. Zum Einsatz kommen hier unterschiedlichste Technologien wie RNV und TNV, ggfs. in Verbindung mit einem Aufkonzentrationsrotor. So können die strikten Grenzwerte der internationalen Luftbehandlungsrichtlinien, wie die der europäischen VOC, eingehalten werden.
Ihre Ansprechpartnerin
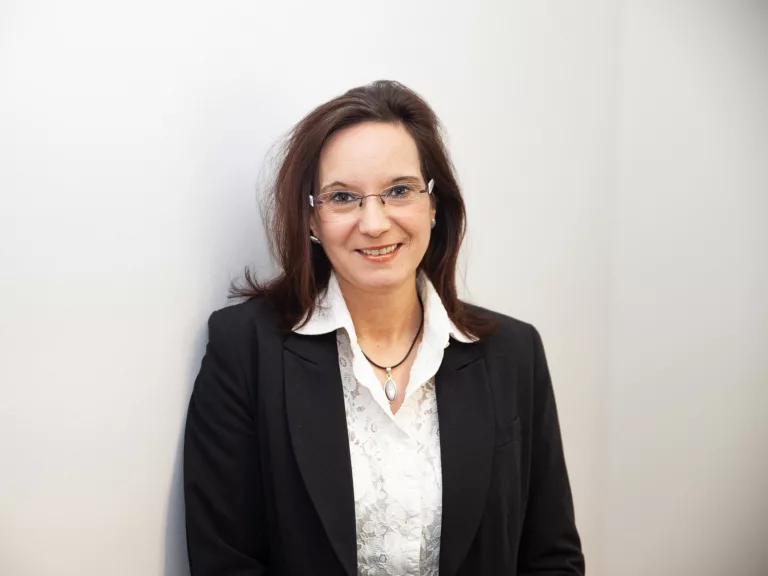